事故案例
2017年12月9日凌晨2点10分左右,某公司二氯苯装置发生爆炸事故,造成10人死亡、1人受伤,直接经济损失高达4875万元。
事故简要经过
2时5分左右,操作工接到内操指令,到1#保温釜进行压料操作。
2时5分31秒,操作工关闭了1#保温釜放空阀,打开压缩空气进气阀用压缩空气(原应使用氮气)向1#高位槽压料。
2时8分41秒,操作工关闭压缩空气进气阀,看到1#保温釜压力快速上升;9分2秒,操作工快速打开1#保温釜放空阀进行卸压;9分30秒,1#保温釜尾气放空管道内出现红光,紧接着保温釜釜盖处冒出淡黑色烟雾。
2时9分49秒,釜内喷出物料发生第一次爆炸;9分59秒,现场发生第二次爆炸。
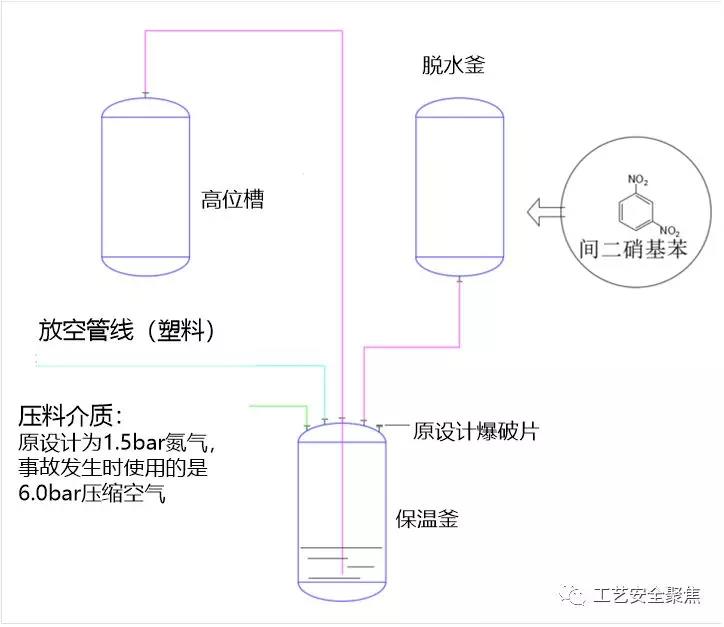
事故直接原因
事故调查报告中明确指出,造成事故的直接原因是:尾气处理系统的氮氧化物(夹带硫酸)窜入1#保温釜,与加入回收残液中的间硝基氯苯、间二氯苯、124-三氯苯、135-三氯苯和硫酸根离子等形成混酸,在绝热高温下,与釜内物料发生化学反应,持续放热升温,并释放氮氧化物气体(冒黄烟);使用压缩空气压料时,高温物料与空气接触,反应加剧(超量程),紧急卸压放空时,遇静电火花燃烧,釜内压力骤升,物料大量喷出,与釜外空气形成爆炸性混合物,遇燃烧火源发生爆炸。
原因分析
该起事故的发生,非常重要的原因之一就是盲目变更,一系列的变更没有执行标准变更流程,且人员安全意识较差,最终导致了悲剧的发生。事故发生所涉及到的变更包括:
介质的变更:擅自更改压料介质,将压料介质由氮气更改为压缩空气;
操作条件的变更:原压料介质压力1.5bar,压缩空气的压力6bar;
安全关键设备的变更:擅自取消了保温釜爆破片,降低了设备安全性能;
工艺变更:擅自改造环保尾气系统,处理后的尾气夹带酸根离子,不符合尾气处理质量要求。
什么是变更管理
所谓变更,指企业在生产经营过程中发生的包括工艺技术、设备设施以及人员管理等方面的永久性或暂时性的变化,而在变更的过程中,可能会产生新的风险。变更管理就是对变更过程进行有计划的管理控制,对变更可能带来的新的风险进行充分的识别和评估,并采取相应的措施消除或控制风险,确保变更过程中和变更后不发生不期望事件。
国外化工企业,对于变更管理工作非常重视,将其纳入工艺安全管理体系。我国也相继出台了一些相关的标准条文,如安监三88号《关于加强化工过程安全管理的指导意见》中指导意见十,明确提出了变更管理的要求。
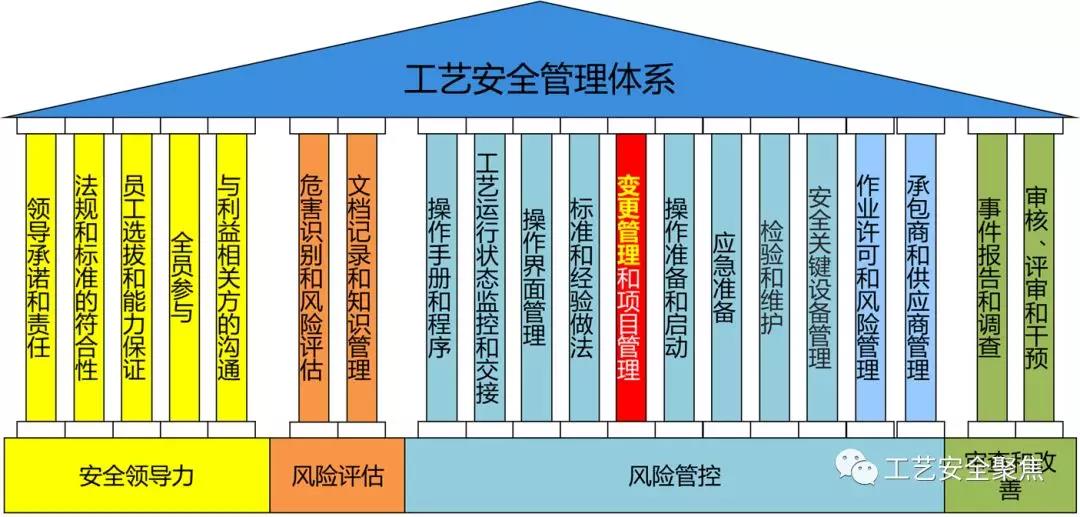
变更管理范围及流程
典型变更管理的范围包括:
资产和设备的变更
操作或操作程序的变更
原材料、产品的变更
组织和人员的变更
软件或控制系统的变更
设计或标准的变更
检修维护中的变更
环境的变更等
变更管理的流程包括:
提出变更并设计变更
变更审查(识别危害)
批准变更
实施变更(施工、培训等)
重新开车(开车流程)
正常运行(操作管理)
相关工艺安全信息更新
变更关闭
变更管理这一要素在实施过程中,并不是孤立的,需要结合PSM中其他要素开展综合管理。

如何提升企业变更管理水平
变更管理是企业实施PSM或安全管理中较难落实的一环,在实施过程中,常见有以下四个方面的问题:
制度和体系:缺乏相关制度和体系,或变更管理制度和体系不够完善,职责范围不清晰等,可执行性较差;
认识和态度:对变更管理的重要性认识不足,执行变更管理上态度不重视,更多是流于表面程序;
能力和资质:相关人员能力或经验不足,不具备相关资质,未能充分识别变更相关风险。
执行和监管:变更管理的执行监管不到位,变更授权随意性大,未能根据风险的高低经由特定的能力资质人员进行批准。
鉴于目前变更管理落实过程中存在的常见问题,建议企业可以从以下几个方面提升变更管理水平:
领导力:加强企业领导力建设,尤其是在变更管理方便的建设。
认知和能力:开展宣讲、培训等,提高企业人员对变更管理重要性、流程、相关风险评估手段等的认识;
制度和体系:建立健全变更管理相关制度,并确保制度切实可行,将变更管理制度并入企业相关管理体系,并定期进行审核和更新;
执行监督:加强监督,将变更管理纳入定期检查和审核关注内容之一,对发现的问题及时进行整改;
目前很多企业变更管理可执行性较差,且企业自身缺乏相关经验知识。这些企业可以通过聘请第三方人员,从制度和体系的建立完善、各种管理工作表的制定、人员意识和能力的培训等方面予以指导或协助,全面提升企业的变更管理水平,这在国外石油化工企业也是非常常见的做法。